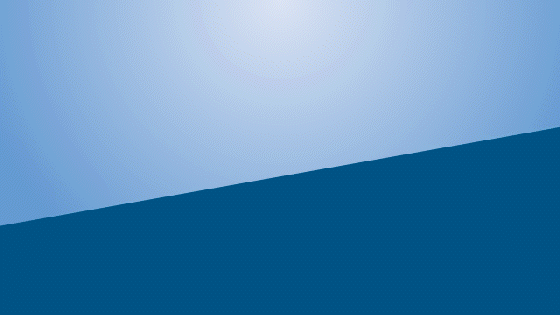
In the contemporary business landscape, prioritizing employee well-being and operational efficiency is imperative for sustained success. While technological advancements have significantly streamlined various operations, the physical demands placed on employees often remain unaddressed. Manual tasks, particularly those involving material handling, can lead to a host of issues including musculoskeletal injuries, decreased morale, and reduced productivity. To mitigate these challenges and create a more conducive work environment, businesses must turn to automation.
By implementing motorized solutions, organizations can significantly enhance employee health and safety. Reducing manual labor through the use of motorized equipment can dramatically decrease the risk of workplace injuries such as back pain, strains, and repetitive stress disorders. This, in turn, contributes to a healthier and more engaged workforce. Moreover, when employees are not burdened by physically demanding tasks, they can dedicate their time and energy to higher-value activities, leading to increased productivity and overall operational efficiency.
The positive impact of motorized solutions extends beyond immediate benefits. By investing in automation, businesses can expect a long-term return on investment through reduced healthcare costs associated with work-related injuries. Additionally, a healthier and more engaged workforce often translates to lower absenteeism rates, further enhancing productivity.
From manufacturing and warehousing to healthcare and hospitality, the applications of motorized solutions are vast and varied. By embracing automation and prioritizing employee well-being, businesses can create a safer, more efficient, and sustainable work environment. Contact PHS West so we can discuss how our motorized solutions can help improve your workplace!